TPS (Toyota Production System) принято считать универсальной, применимой к любой отрасли с небольшой адаптацией под конкретные условия. Однако внедрить ее в России и добиться существенных результатов пока удалось немногим. Например, заводу «КамАЗ», который за шесть лет с момента внедрения (2008 год) сократил издержки более чем на 30 млрд рублей. Или «Сбербанк», который за два года в четыре раза увеличил розничные продажи, сократив время ожидания в очередях на 36%.
Сложности при внедрении TPS в России
Несмотря на то, что в России единые подходы к внедрению бережливого производства поддерживаются приказом Минпромторга, существуют сложности внедрения TPS на предприятиях. Например, противоречивая терминология, сложности в финансово-экономическом состоянии предприятий, нехватка средств и ресурсов для преобразований и неприятие изменений сотрудниками компаний.
Многие российские предприятия, пытаясь улучшить производство, используют лишь несколько отдельных инструментов TPS, а не всю концепцию комплексного внедрения. Такой подход вряд ли приведет к ощутимым результатам.
Ситуация осложняется нехваткой опытных специалистов. Многочисленные самозваные «эксперты по бережливому производству», прочитав несколько книг по теме, берут на себя ответственность давать рекомендации по изменению бизнес-процессов, которых они не понимают. В результате внедрение срывается, эффект в лучшем случае не оказывается отрицательным, а руководители компаний приходят к убеждению, что «бережливое мышление» – обычное мошенничество. Я дважды сталкивался с последствиями работы таких «экспертов». Собственники компаний, заслышав от меня фразу «производственная система Toyota», начинали нехорошо улыбаться и быстро сворачивали разговор. Потом наводили обо мне справки у меня за спиной – не обманщик ли я. Причем в первом случае убедить человека, что в его же интересах вернуться к TPS, так и не удалось, несмотря на хорошие рекомендации от уважаемых им людей.
Кроме того, благодаря книгам и статьям о TPS, в которых пишут о резких улучшениях, многие российские производители рассчитывают на получение быстрых результатов от внедрения производственной системы в течение шести-восьми месяцев. Никому не хочется думать о том, что у Toyota на создание и отладку системы ушло несколько десятилетий. В реальности внедрение TPS в полном объеме займет несколько лет, хотя первый эффект проявится достаточно быстро. Когда опытные специалисты по бережливому производству, например, Джеймс Вумек и Дэниел Джонс, пишут, что что-то не так, если вы не получаете ощутимых результатов через две-три недели, речь идет об отдельных усовершенствованиях.
Ошибка 1: слепое копирование чужого успеха
Многие компании при внедрении TPS пытаются слепо копировать наработки в области процессов, в то время как в Toyota система является в первую очередь философией компании. Это скорее набор примеров, по которому можно опознать проблемы, актуальные для любой компании.
Принципы управления, описанные Джеффри Лайкером, также не универсальны. Классический список потерь Toyota и инструменты их устранения формировались на основе практической деятельности корпорации – для рынка автопрома. Поэтому, например, слепое следование созданию потока единичных изделий при организации производства в строительной компании может противоречить логике деятельности организации. Потому что при строительстве дома единичным изделием является квартира. Никто не будет строить дом поквартирно.
Приведу пример неудачной попытки слепого копирования TPS. В крупной строительной компании со штатом свыше тысячи сотрудников было принято решение о внедрении системы бережливого производства. Был привлечен специалист, который заставлял сотрудников учить наизусть принципы TPS, названия видов потерь и инструментов борьбы с ними. Во время обучения команда имитировала поток единичных изделий, решала абстрактные задачи, подгоняя реальные проблемы под потери из списков Toyota.
С момента внедрения «улучшений» эффективность работы компании снизилась на 18%. Ситуацию удалось спасти, изменив подход к внедрению. Во главу угла встали новые корпоративные принципы, 8, а не 14, которые были адаптированы под деятельность компании. Сотрудников просили не учить наизусть список потерь Toyota, а искать их самостоятельно на предприятии. Через полгода удельная прибыль на одного сотрудника выросла на 22-23%.
Ошибка 2: игнорирование потока создания ценности
Часто организации, начинающие внедрять у себя бережливое производство, сосредотачиваются на улучшении отдельных процессов, поток создания ценности «протекает» по ряду подразделений, для каждого отдельного потока назначается ответственный, но за поток в целом никто не отвечает. В такой ситуации части потока оптимизируются в отрыве от основного. Это значительно снижает эффективность усовершенствований и в ряде случаев может принести вред компании. Комплексного изменения не происходит, более того, может разрушиться уже возникший баланс между процессами.
Подразумевается, что результаты по отдельным процессам будут впоследствии объединены в карту создания ценности. Но при таком подходе удается получить лишь организационную схему предприятия, а не карту потока производимых продуктов. Это позволит оптимизировать штат, а не рабочие процессы и поток создания ценности.
Чтобы этого не произошло, необходимо назначить менеджера общего потока, который будет подчиняться руководителю, отвечать за внедрение бережливого производства, производить изменения в функциональных и структурных подразделениях, составлять, реализовывать и периодически корректировать план внедрения изменений, расставлять приоритеты, руководить разработкой карт потока и вести наблюдение за всеми сторонами внедрения.
При этом стоит помнить, что исключение потерь на уровне подразделений не менее важно, чем на уровне всего потока. Просто во втором случае эффект будет более масштабным, так как охватит предприятие в целом.
Ошибка 3: отсутствие вовлеченности персонала
Ключевые составляющие успеха TPS – люди и процессы. Главная роль у людей – именно они создают и поддерживают процессы и системы. Однако в России люди часто создают больше проблем, чем способствуют успеху внедрения. Ведь в большинстве компаний организационная структура вертикальная, в отличие от плоской у Toyota. Это создает необходимость сотрудникам подниматься на несколько уровней выше для решения и согласования вопросов, которые находятся в собственной компетенции. При этом обеспечивающие подразделения, отделы кадров, IT-службы, юристы, а также возложенные на производства контрольно-отчетные функции не всегда способствуют быстрому решению вопросов.
Важно, чтобы все сотрудники компании содействовали работе групп и помогали специалистам производственных подразделений, генерирующих добавленную стоимость. Для успешного внедрения при обучении должны разбираться проблемы, взятые из реальной трудовой жизни сотрудников и мешающие именно им работать более успешно. Желательно изучать мнения и настроения сотрудников, принимать меры по росту вовлеченности в процесс (убеждение, нематериальное стимулирование, главное – не принуждение), поощрять инициативу.
При формировании команд важно обеспечить взаимозаменяемость и взаимодополняемость сотрудников, потому что успех зависит не от отдельных людей, но от их совместных действий. Построение команды – достаточно серьезная задача, которая решается индивидуально в зависимости от культуры компании.
Будущее TPS в России
В России насчитывается несколько десятков предприятий, находящихся на различных этапах развития производственных систем и обладающих тем или иным опытом во внедрении. Это группы компаний «ГАЗ», «Иркут», «Русал», «Росатом» и ряд других.
Основываясь на личном опыте, я смело могу утверждать, что TPS может быть применена практически в любых организациях, независимо от формы собственности и отрасли. Главное – адаптировать ее под нужды компании, избегать ключевых ошибок и использовать накопленный российский опыт.
Андрей! Не знаю, уловили ли вы смысл в слове Platform. Что касается Smart Manufacturing - я знаю работы немецких авторов, более ранние, чем концепция MIP. Если хотите, то я могу "сие" или "оное" и "таковое" подтвердить ссылками (но на немецком).
Cам термин интегральный или "сквозной" софт мы обсуждали на MES-форуме лет 5 назад. Речь идет не об идеях, а о разработанной и утвержденной концепции, оцененной экспертами и получившей национальную премию по инновационным направлениям INNOVATIONSPREIS-IT 2018
но я сразу "уловил" смысл - за большие деньги, а я сам участвую в обсуждении бесплатного опыта в японских методах работы ))) И вы пропустии главный посыл:
Андрей Радионов пишет: Будущее за Smart Manufacturing - Умным производством.
Если вы внимательно прочитаете книги о Производственной системе Тойоты - Toyota Production System - TPS, то увидите систему, большинство характеристик которой уже можно было давно отнести к работающему образцу такой системы. Эта система уже многие годы соответствует тому, что сейчас называют Индустрия 4.0
... я вроде бы об этом не писал. Я писал, в частности, что в Германии многое делается за государственные деньги, есть много программ.
Мы же (за свои деньги) сейчас решаем более скромную задачу - создание универсальной информационной шины предприятия (что является одной из составных частей smart factory), а также своей BI-cистемы.
Со многими реально современнми предприятиями я, поверьте, знакомлюсь не по книгам, а посещая их, участвуя в совместных проектах
Некоторые книги стоит читать, особенно, если ряд ваших коллег, которые приняли активное участие в этой дискуссии, называют производство на всех заводах Toyota массовым. ))) - Вы тоже не возражали им здесь и в дискуссии на форуме МЕS - наверное, это запутало не одного вашего читателя ))) Стоит обратить вниманиег, что базовый принцип Toyota - поток единичных изделий. Даже приводил примеры как работает у них конвейер, но даже это не помогло - как в фильме "ложат, и ложат" )))
https://www.youtube.com/watch?v=9MRzt4ycxjM
Чтобы понять, как работает Toyota Production System, стоит начать с книги Тайити Оно "Производственная система Тойоты: уходя от массового производства" - японцы и начинали не с массового производства, и никогда не переходили на него, за некоторым исключением. Но при этом стремились к эффективности Like - подобно массовому, и им это удалось на многих заводах.
Ну, у нас все решают некомпетентные люди типа Грефа, завтра решат что SAP, то быстро договорятся с немчурой, откроют тут какую нить фирму и от ее имени будут всем всучивать SAP в очередной раз.
Потому мне тут неинтересно, хорошо бы выйти на ухоженные рынки немцев, япошек... это требует некоторое количество бабла и т.д., что пока проблемно.
Евгений, не знаю в чём и где вы видите смысл в этом споре, когда японцы давно уже определились с тем, что у них не массовое производство ))) - поток единичных изделий.
Удалось найти ссылку, в которой упоминается - "Финальные операции ))) по сборке автомобилей Лада Гранта и Лада Калина на конвейере"
Кстати, если сравнить с тем, как работают на заводе Toyota, то можно увидеть сколько бесполезных людей стоит рядом с конвейером в России (((
https://www.fassen.net/video/6Xdds-UX_AA/
и сравним - Япония Завод Toyota - 2005: Нет рабочих, как в примере выше, которые просто стоят, много разговаривают или медленно слоняются по цеху. При этом ещё и шума в 10 раз меньше.
https://www.youtube.com/watch?v=pcgcsPOrGIc&feature=youtu.be
Чем ещё полезны японские методы - Чтобы люди работали интенсивно и не слонялись без дела.
1. Вот если бы на этом конвейере собирали одновременно пылесосы, люстры и автомобили - то это можно было бы называть потоком единичных изделий (и то с натягом). (это воще то легко делается, если ТП и мощности соответствуют)
2. Что бы все работали интенсивно (не только люди, но и все простаивающие мощности) надо иметь компактное расписание работ, что требует применение мощных алгоритмов составления плана работ.
так сразу и представил, как вы бегаете по цеху с этой распечаткой, сложенной в трубочку, и подгоняете всех работников )))
Может быть я не понял, что Евгений имел в виду под "на этапе финальной сборки" ))) - или это означает, что все отдыхают и празднуют?
Андрей Радионов пишет: Удалось найти ссылку, в которой упоминается - "Финальные операции ))) по сборке автомобилей Лада Гранта и Лада Калина на конвейере" Кстати, если сравнить с тем, как работают на заводе Toyota, то можно увидеть сколько бесполезных людей стоит рядом с конвейером в России (((
https://www.fassen.net/video/6Xdds-UX_AA/
ну, когда сказать нечего и не то померещится :)
мне пофиг как там ладу собирают, я за державу не отвечаю
мне на Яндексе, Рамблере и т.п. нативная реклама надоела - не знаешь уже куда податься - это моя реакция на этом ресурсе на вашу с коллегами - не то ещё померещится
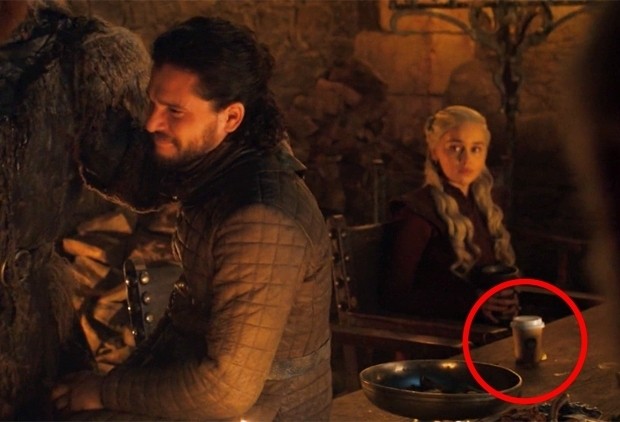
https://www.e-xecutive.ru/management/marketing/1990657-nativnoi-reklamy-budet-esche-bolshe-i-ot-etogo-vse-proigraut Нативной рекламы будет еще больше, и от этого все проиграютЦитата из статьи: "Рано или поздно наступит момент, когда и редакциям, и рекламодателям захочется сказать «Так, теперь серьезно. Вот это правда!». Но уже никто не поверит. Больше не останется форматов и площадок, гарантирующих объективность. Не останется настолько доверчивых людей, чтобы общаться с ними напрямую, минуя встроенный в черепную коробку спам-фильтр.
Самое обидное, что эта волна последствий накроет всех без исключения".